Double Beam EOT (Electric Overhead Travelling) Cranes are essential assets in various industries, providing efficient lifting and transportation of heavy loads. Over time, wear and tear can impact their performance, necessitating meticulous repairs to ensure optimal functionality. In this comprehensive guide, we will explore six key points crucial for effectively repairing a double beam EOT crane, covering aspects from structural integrity to electrical systems.
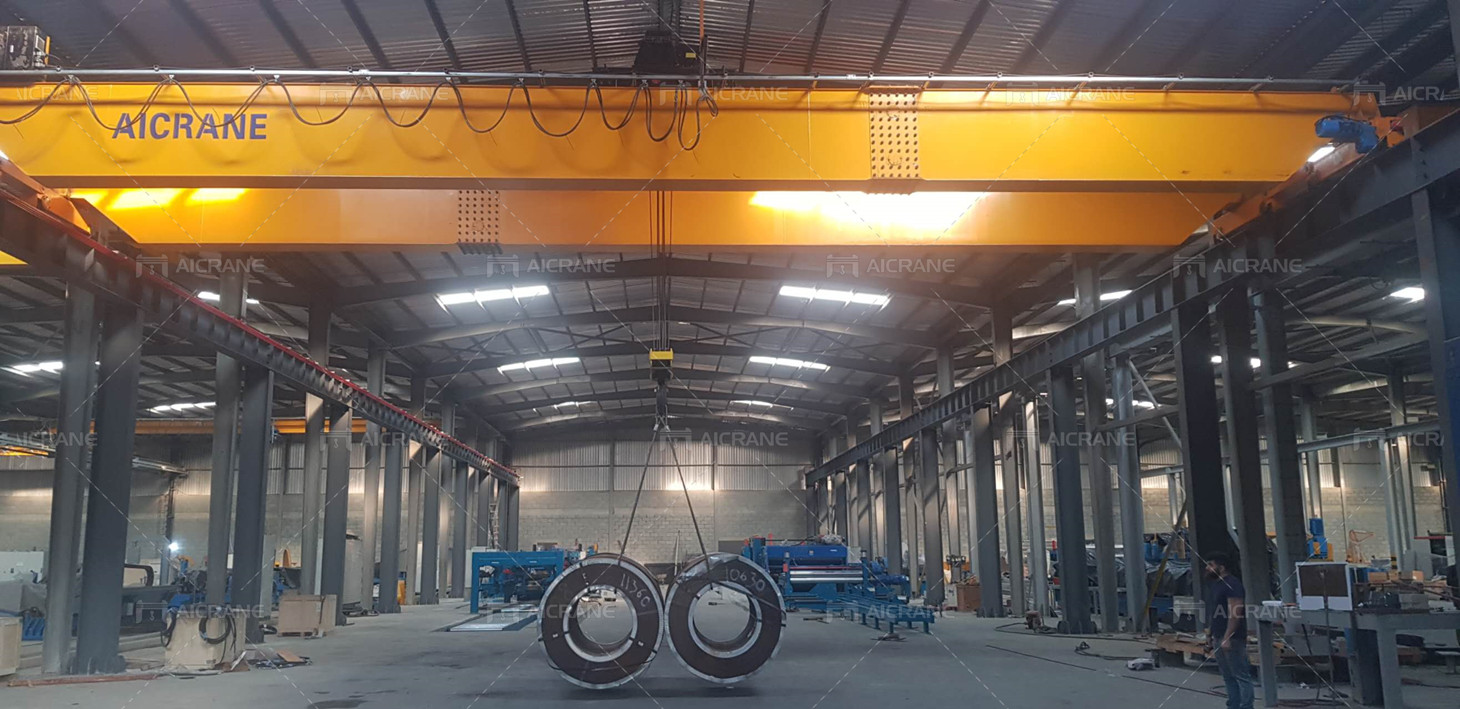
Thorough Structural Inspection
The structural components of a double beam EOT crane bear the brunt of heavy loads and continuous operations. Regular and thorough inspections are imperative to identify signs of wear, corrosion, or structural deformities. The inspection should encompass the double beams, end carriages, and the crane’s main frame of the overhead crane.
If any issues are detected, structural repairs and welding may be necessary. Welding should be conducted by certified professionals, adhering to industry standards and the specifications of the crane manufacturer. Post-welding, non-destructive testing (NDT) methods such as ultrasonic or magnetic particle testing should be employed to ensure the integrity of the welds.
Overhaul of Trolley and Hoisting Mechanisms
The trolley and hoisting mechanisms are critical for the precise lifting and movement of loads. Over time, components like wire ropes, hooks, and sheaves can experience wear and tear, affecting the efficiency of these mechanisms.
Inspect wire ropes for signs of wear, kinks, or deformities. Replace worn-out wire ropes promptly to prevent potential failures during lifting operations. Examine hooks for any deformation or wear, and replace them if necessary. Ensure sheaves are in proper alignment to prevent uneven wear on the wire ropes.
Consider a comprehensive overhaul of the hoisting mechanism, including checks on the brakes and associated systems. Functional brakes are crucial for controlled movements and preventing unintended descent.
In-Depth Evaluation of the Electrical System
The electrical system is the nerve center of a double beam EOT crane, comprising motors, control panels, limit switches, and sensors. Routine evaluations are necessary to identify issues like loose connections, damaged cables, or malfunctioning components.
Inspect all electrical connections and wiring for wear, damage, or corrosion. Promptly replace any damaged cables or wires to prevent electrical faults. Verify the functionality of control panels, ensuring buttons, switches, and indicators operate smoothly.
Consider upgrades to the electrical system with modern components or control systems. Upgraded systems often offer improved efficiency, advanced features, and better diagnostic capabilities.
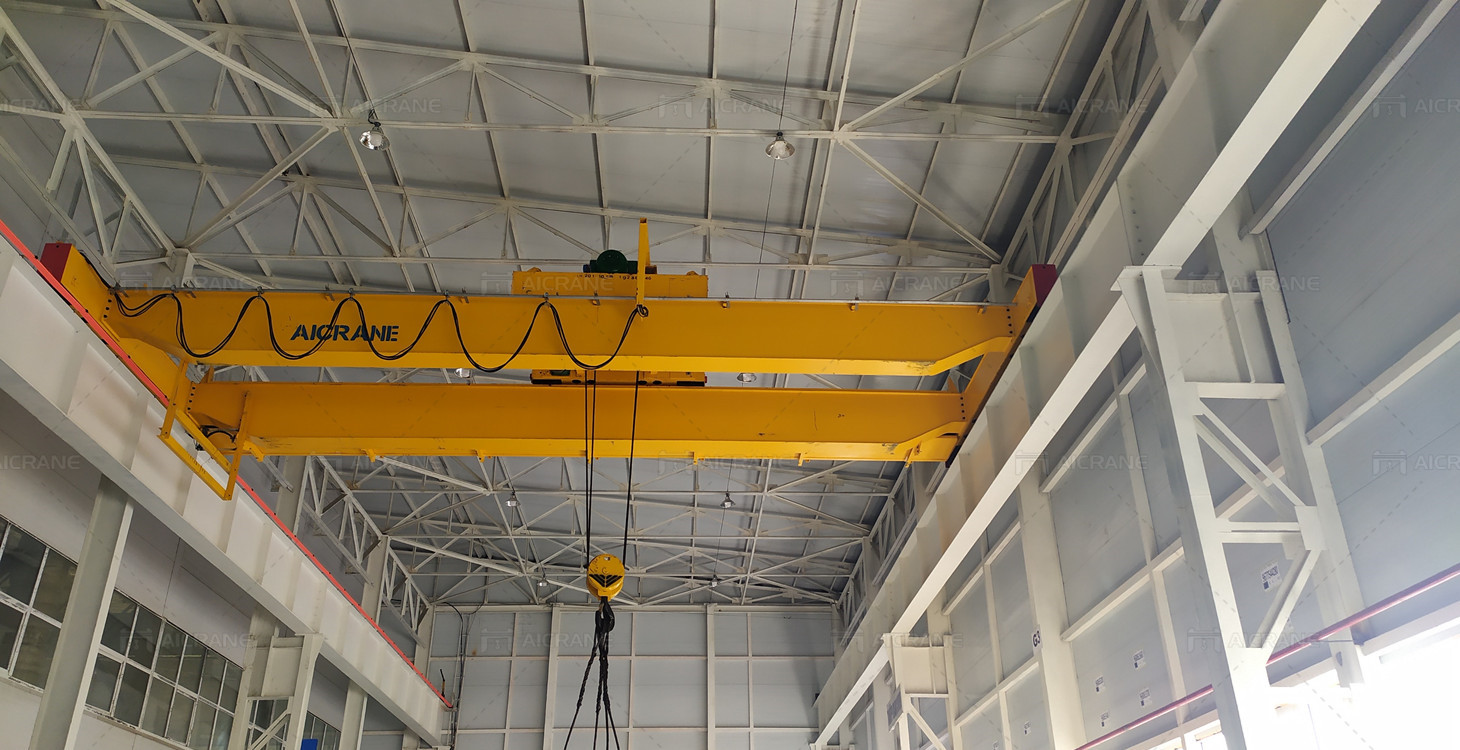
Examination and Maintenance of Wheels and Wheel Assemblies
Wheels and wheel assemblies are integral to the mobility and stability of a double beam EOT crane. Regular inspections should be carried out to identify wear, misalignment, or other issues affecting the wheels.
Check for signs of wear on the wheels and rails, and promptly replace any worn-out components. Misalignment issues should be addressed to ensure smooth movements along the runway. Lubricate wheel assemblies regularly to reduce friction and minimize wear.
Consider implementing a preventive maintenance schedule for wheels, including inspections, lubrication, and timely replacements. Well-maintained wheels contribute to the overall stability and longevity of the crane.
Assessment and Upgrade of Control Systems
Control systems play a vital role in the precision and safety of double beam EOT cranes. Evaluate the performance of the control systems, including programmable logic controllers (PLCs) and other electronic components.
Identify outdated or obsolete control systems that may hinder the crane’s efficiency. Consider upgrading to modern control systems that offer enhanced features, improved diagnostics, and compatibility with advanced technologies.
Ensure that control systems are calibrated accurately to provide precise control during lifting and movement operations. Regularly update software and firmware to benefit from the latest advancements in crane control technology.
Alignment and Calibration Procedures
Proper alignment is crucial for the smooth and efficient operation of a double beam EOT crane. Misalignments in the double beams, end trucks, or trolley mechanisms can lead to uneven stress distribution, increased wear, and compromised safety.
During the repair process, ensure that all structural components are correctly aligned. Check the alignment of the double beams and verify that the end trucks move smoothly along the runway. Examine the trolley mechanism to ensure it moves parallel to the beams without deviations.
After structural repairs and alignment adjustments, calibrate the crane’s controls and load indicators. Calibration ensures accurate readings and precise control during lifting operations. Follow the manufacturer’s guidelines for calibration procedures and conduct regular checks to maintain accuracy.
Effectively repairing a double beam EOT crane requires a systematic approach, addressing structural, mechanical, and electrical components. The key points discussed—thorough structural inspection, overhaul of trolley and hoisting mechanisms, in-depth evaluation of the electrical system, examination and maintenance of wheels and wheel assemblies, assessment and upgrade of control systems, and alignment and calibration procedures—constitute a holistic strategy for ensuring the crane’s optimal performance and longevity.
By implementing these key points in the repair process, operators and maintenance personnel can not only address existing issues but also enhance the overall safety, efficiency, and reliability of double beam EOT cranes. Regular maintenance and prompt repairs contribute to minimizing downtime, preventing accidents, and maximizing the return on investment in various industrial applications.