Selecting the right rail-mounted crane is a critical decision that can significantly impact the efficiency and safety of material handling operations in various industries. Rail-mounted cranes, also known as gantry cranes, are widely used for lifting and moving heavy loads in locations such as shipyards, ports, and manufacturing facilities. Choosing the appropriate rail-mounted crane involves considering several key factors to ensure it aligns with the specific requirements of the application. In this comprehensive guide, we will explore the step-by-step process of choosing a rail-mounted crane.
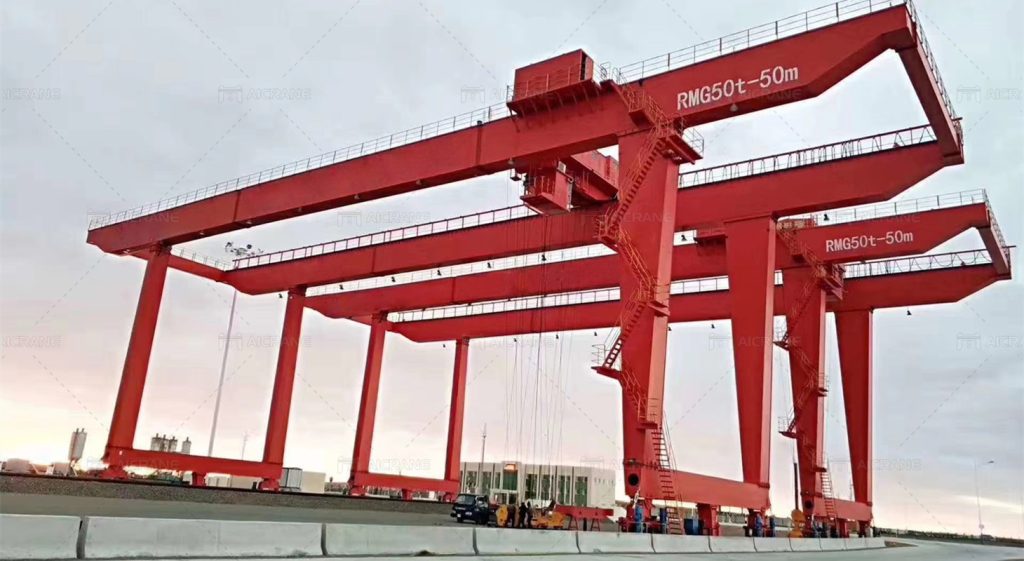
Define the Application Requirements
Before diving into the selection process, it’s crucial to clearly define the application requirements. Consider the following aspects:
Lifting Capacity: Determine the maximum weight that the rail-mounted crane needs to lift. Ensure that the crane’s capacity aligns with the heaviest loads anticipated in the application.
Span and Coverage: Evaluate the span and coverage required to effectively reach and lift loads within the designated workspace. Consider the layout of the facility and the specific areas where the crane will be operating.
Lifting Height: Determine the lifting height needed to accommodate stacking or unstacking tasks. Consider the vertical space available in the facility and any height restrictions.
Duty Cycle: Assess the duty cycle or the frequency of crane operation. Some applications may require continuous operation, while others may involve intermittent or occasional use.
Choose the Right Type of Rail-Mounted Crane
Rail-mounted cranes come in various types, each designed for specific applications. Consider the following types based on their characteristics:
Single Girder vs. Double Girder: Single girder cranes are suitable for lighter loads and shorter spans, while double girder cranes offer higher lifting capacities and are ideal for longer spans.
Top Running vs. Under Running: Top running cranes travel on rails installed on the top of the runway beams, providing greater hook height. Under running cranes run on rails mounted beneath the runway beams, making them suitable for facilities with limited headroom.
Rubber Tired Gantry (RTG) Crane: RTG cranes are mobile and use rubber tires for movement. They are suitable for container handling in ports and container yards.
Rail Mounted Gantry (RMG) Crane: RMG cranes are fixed and move along rails. They are commonly used in rail-served container yards and offer precise container positioning.
Consider Rail Type and Layout
Evaluate the type of rail system in the facility and the layout of the rails:
Gauge and Rail Size: Ensure that the crane’s rail gauge matches the existing rail system in the facility. Consider the size and strength of the rails to support the crane’s load.
Rail Layout and Configuration: Analyze the configuration of the rail system, including straight tracks, curves, switches, and crossovers. Choose a rail-mounted crane that can navigate the specific layout of the rail system.
Power Supply: Determine the availability and type of power supply for the crane. Rail-mounted cranes can be powered by electricity, diesel, or a combination of both, depending on the application and infrastructure.
Evaluate Operational Speed and Control
Operational speed and control are crucial factors in optimizing material handling efficiency:
Hoisting Speed: Consider the hoisting speed of the crane, especially if rapid vertical movements are essential for the application. Faster hoisting speeds can contribute to increased productivity.
Travelling Speed: Assess the travelling speed of the crane along the rails. Faster travelling speeds are beneficial for reducing cycle times and improving overall operational efficiency.
Trolley Speed: Evaluate the speed of the trolley, which moves horizontally along the bridge or girder. A well-balanced trolley speed is important for precise load positioning.
Control Systems: Choose a rail-mounted crane with advanced control systems that offer precision, reliability, and ease of use. Features such as variable frequency drives and programmable logic controllers contribute to efficient control.
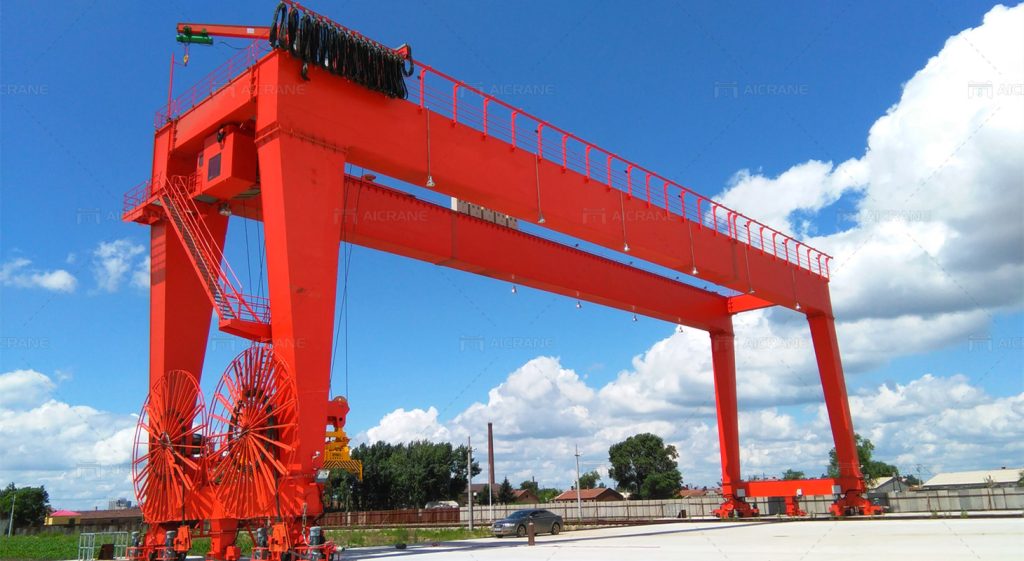
Safety Features and Compliance
Safety is paramount in material handling operations, and rail-mounted cranes should be equipped with robust safety features:
Overload Protection: Ensure the crane is equipped with an overload protection system to prevent the crane from lifting loads beyond its rated capacity.
Emergency Stop Mechanism: Verify the presence of an emergency stop mechanism that can quickly halt all crane movements in case of an emergency.
Limit Switches: Incorporate limit switches to prevent the crane from exceeding specified travel limits and ensure safe operation within defined parameters.
Collision Avoidance Systems: Consider cranes with collision avoidance systems to prevent collisions with obstacles or other cranes, enhancing overall safety.
Compliance with Standards: Ensure that the selected rail-mounted crane complies with relevant industry standards, local regulations, and safety guidelines.
Environmental Considerations
Take into account the environmental conditions in which the rail-mounted crane will operate:
Corrosion Resistance: If the crane will be exposed to corrosive environments, choose materials and coatings that offer resistance to corrosion, extending the crane’s lifespan.
Weather Protection: Consider weatherproofing features to protect the crane from adverse weather conditions, especially if it will be operating outdoors.
Temperature Tolerance: Assess the crane’s tolerance to temperature extremes, especially in environments with high or low temperatures.
Lifecycle Costs and Maintenance
Evaluate the long-term costs associated with the rail-mounted crane, including maintenance and operational expenses:
Maintenance Requirements: Choose a crane with minimal maintenance requirements, reducing downtime and overall maintenance costs.
Serviceability: Ensure that the crane is designed for ease of serviceability, with accessible components for routine inspections and repairs.
Lifecycle Costs: Consider the total cost of ownership, factoring in initial costs, maintenance expenses, and energy consumption over the crane’s expected lifespan.
Supplier Reputation and Support
Select a reputable and reliable supplier for the rail-mounted crane:
Supplier Experience: Choose a supplier with a proven track record and extensive experience in manufacturing and delivering rail-mounted cranes.
Customer References: Seek references from previous customers to gauge the supplier’s performance in terms of product quality, reliability, and after-sales support.
After-Sales Support: Ensure that the supplier offers comprehensive after-sales support, including maintenance services, spare parts availability, and technical assistance.
Customization Options
Assess the availability of customization options to tailor the rail-mounted crane to specific application requirements:
Custom Configurations: Choose a supplier that offers customization options for crane configurations, such as varying spans, lifting heights, and trolley configurations.
Specialized Attachments: Consider the availability of specialized attachments or features that may be required for unique material handling tasks.
Regulatory Compliance and Documentation
Verify that the selected rail-mounted crane complies with relevant industry standards and obtain comprehensive documentation:
Certifications: Ensure that the crane meets necessary certifications and compliances, such as CE certification or other regional standards.
Documentation: Obtain detailed documentation, including user manuals, maintenance guides, and safety specifications.
Choosing the right rail-mounted crane involves a thorough assessment of application requirements, rail systems, operational characteristics, safety features, and supplier reputation. By carefully considering these factors, businesses can make informed decisions that align with their specific material handling needs. Regular maintenance, compliance with safety standards, and ongoing support from the supplier contribute to the long-term success and efficiency of the rail-mounted crane in various industrial settings. Contact the crane manufacturer to get more information.